APQP (Erweiterte Produktqualitätsplanung)
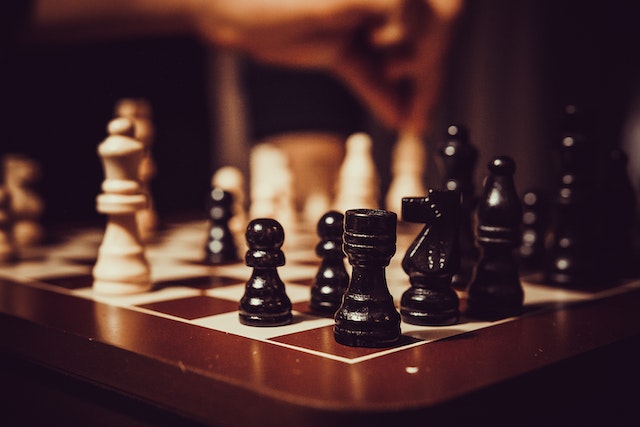
- 4348
- 115
- Lewis Holzner
Was ist der APQP?
APQP (Erweiterte Produktqualitätsplanung), In spanischer "fortschrittlicher Produktqualitätsplanung" ist ein Rahmen für Verfahren und Techniken, die zur Entwicklung von Produkten in der Branche verwendet werden, insbesondere in der Automobilfuhr.
Komplexe Versorgungsprodukte und -ketten haben viele Möglichkeiten, insbesondere wenn neue Produkte eingeführt werden. APQP ist ein strukturierter Prozess für die Gestaltung von Produkten und Prozessen, die darauf abzielt, die Kundenzufriedenheit mit neuen Produkten oder Prozessen zu gewährleisten.
Dieser Ansatz verwendet Tools und Methoden, um die mit Änderungen in einem neuen Produkt oder Prozess verbundenen Risiken zu verringern.
Ziel ist es, einen standardisierten Plan für Produktqualitätsanforderungen zu erstellen, der Lieferanten ein Design ermöglicht, das den Kunden zufriedenstellt und die Kommunikation und Zusammenarbeit zwischen verschiedenen Aktivitäten erleichtert.
Im APQP -Prozess wird ein multifunktionales Gerät verwendet, das Marketing, Produktdesign, Einkäufe, Produktion und Vertrieb umfasst. Dieser Prozess wird von General Motors, Ford, Chrysler und ihren Lieferanten für sein Produktentwicklungssystem verwendet.
APQP -Phasen
APQP dient als Leitfaden im Entwicklungsprozess und auch als Standard, um Ergebnisse zwischen Lieferanten und Automobilunternehmen zu teilen. Es besteht aus fünf Phasen:
Phase 1: Planung und Definition des Programms
Wenn die Kundennachfrage die Einführung eines neuen Produkts oder die Überprüfung eines vorhandenen erfordert, wird die Planung zu einem zentralen Thema, noch vor den Diskussionen über das Design oder die Neugestaltung des Produkts.
In dieser Phase versucht die Planung, die Kundenbedürfnisse und auch die Erwartungen des Produkts zu verstehen.
Zu den Planungsaktivitäten gehört das Sammeln der erforderlichen Daten, um zu definieren, was der Kunde wünscht.
Kann Ihnen dienen: Primärsektor: Merkmale, wirtschaftliche Aktivitäten, BedeutungDann können Sie das Qualitätsprogramm definieren, das zum Erstellen des Produkts wie angegeben erforderlich ist. Das Ergebnis dieser Arbeit umfasst Produktdesign, Zuverlässigkeit und Qualitätsziele.
Phase 2: Produktdesign und -entwicklung
Der Zweck dieser Phase besteht darin, das Produktdesign zu vervollständigen. Hier finden Sie auch eine Bewertung der Lebensfähigkeit der Produkte. Die Ergebnisse aus der Arbeit in dieser Phase umfassen:
- Überprüfung und Überprüfung des abgeschlossenen Designs.
- Definierte Spezifikationen von Gerätematerialien und Anforderungen.
- Effektanalyse- und Entwurfsausfallmodus abgeschlossen, um die Fehlerwahrscheinlichkeiten zu bewerten.
- Kontrollpläne für die Erstellung des Produktprototyps.
Phase 3: Design und Entwicklung des Produktherstellungsprozesses
Diese Phase konzentriert sich auf die Planung des Herstellungsprozesses, der das neue oder verbesserte Produkt erzeugt.
Ziel ist es, den Produktionsprozess zu entwerfen und zu entwickeln, wobei die Spezifikationen und die Produktqualität sowie die Produktionskosten berücksichtigt werden.
Der Prozess muss in der Lage sein, die erforderlichen Beträge zu erzeugen, um den erwarteten Nachfrage der Verbraucher zu decken, während die Effizienz beibehalten wird. Die Ergebnisse in dieser Phase umfassen:
- Eine vollständige Prozessflusskonfiguration.
- Eine Effekt- und Fehleranalyse des vollständigen Prozesses zur Identifizierung und Verwaltung von Risiken.
- Qualitätspezifikationen des Betriebsprozesses.
- Produktverpackung und Bearbeitung Anforderungen.
Phase 4: Prozess- und Produktvalidierung
Es ist die Testphase, um den Herstellungsprozess und das Endprodukt zu validieren. Die Schritte umfassen:
- Bestätigung der Kapazität und Zuverlässigkeit des Produktionsprozesses. Ebenso das Kriterium zur Annahme der Produktqualität.
Kann Ihnen dienen: Einfaches Interesse: Elemente, wie man es berechnet und Beispiel- Realisierung der Testproduktionsläufe.
- Produkttest zur Bestätigung der Wirksamkeit des implementierten Produktionsansatzes.
- Vereinbaren Sie die erforderlichen Anpassungen, bevor Sie in die nächste Phase übergehen.
Phase 5: Start, Bewertungen und kontinuierliche Verbesserung
In dieser Phase erfolgt die Einführung der großflächigen Produktion, die die Bewertung und Verbesserung der Prozesse betont.
Zu den Säulen dieser Phase gehören die Verringerung der Prozessschwankungen, die Identifizierung von Problemen und der Beginn von Korrekturmaßnahmen zur Unterstützung der kontinuierlichen Verbesserung.
Es gibt auch die Erfassung und Bewertung des Kundenfeedbacks und der Daten im Zusammenhang mit der Effizienz des Prozesses und der Qualitätsplanung. Die Ergebnisse umfassen:
- Ein besserer Produktionsprozess durch Reduzierung von Prozessvariationen.
- Qualitätsverbesserung der Produktlieferung und des Kundendienstes.
- Verbesserung der Kundenzufriedenheit.
Beispiel
Wo kann APQP einbezogen werden
- Entwicklung von Anforderungen aus der Stimme des Kunden unter Verwendung der Implementierung der Qualitätsfunktion.
- Entwicklung eines Produktqualitätsplans, der in den Projektplan integriert ist.
- Produktdesignaktivitäten, die spezielle oder wichtige Merkmale zur Verarbeitung von Designaktivitäten vermitteln, bevor das Design befreist. Dies umfasst neue Formen und Teile, engere Toleranzen und neue Materialien.
- Entwicklung von Prozessplänen.
- Verwendung einer formellen Entwurfsprüfung zur Überwachung des Fortschritts.
- Planung, Erfassung und Installation geeigneter Geräte und Werkzeuge gemäß den von der Produktdesignquelle angegebenen Designtoleranzen.
Kann Ihnen dienen: Wirtschaftsinstitutionen: Merkmale, Beispiele, Ziele- Vorschlag Kommunikation durch Montage- und Fertigungspersonal auf die Möglichkeiten, ein Produkt besser zusammenzustellen.
- Festlegung geeigneter Qualitätskontrollen für besondere Merkmale oder Tasten eines Produkts oder Parameter eines Prozesses, die weiterhin das Risiko potenzieller Fehler ausmachen.
- Stabilitätsstudien und Kapazität spezieller Merkmale durchführen, um die vorliegende Variation zu verstehen und somit zukünftige Leistung mit statistischer Prozesskontrolle und Prozesskapazität vorherzusagen.
Branchen, die es nutzen
Ford Motor Company veröffentlichte das erste Handbuch für fortschrittliche Qualitätsplanung für seine Lieferanten in den frühen 80ern. Dies half den Ford -Lieferanten, angemessene Kontrollen für die Prävention und Erkennung neuer Produkte zu entwickeln, wodurch die Qualitätsanstrengungen unterstützt werden.
Am Ende der 80er Jahre verwendeten die Haupthersteller der Automobilindustrie in den USA APQ -Programme. General Motors, Ford und Chrysler hatten es implementieren und sahen dann die Notwendigkeit, sich beizutragen, um für ihre Lieferanten einen Common -Kern der Prinzipien der Produktqualitätsplanung zu schaffen.
Die Richtlinien wurden Anfang der 90er Jahre festgelegt, um sicherzustellen, dass APQP -Protokolle mit einem standardisierten Format fortgesetzt werden.
Die Vertreter der drei Automobilhersteller und der American Society for Quality Control haben eine Gruppe von Qualitätsanforderungen geschaffen, um ein gemeinsames Verständnis von Fragen von gegenseitigem Interesse innerhalb der Automobilindustrie zu haben.
Diese Methodik wird jetzt auch von progressiven Unternehmen verwendet, um Qualität und Leistung durch Planung zu gewährleisten.
Verweise
- Fortgeschrittene Produktqualitätsplanung. Entnommen von NPD-Lösten.com.
- Erweiterte Produktqualitätsplanung (APQP). Von Qualität entnommen -eins.com.