Toyotismusgeschichte, Merkmale, Vor- und Nachteile
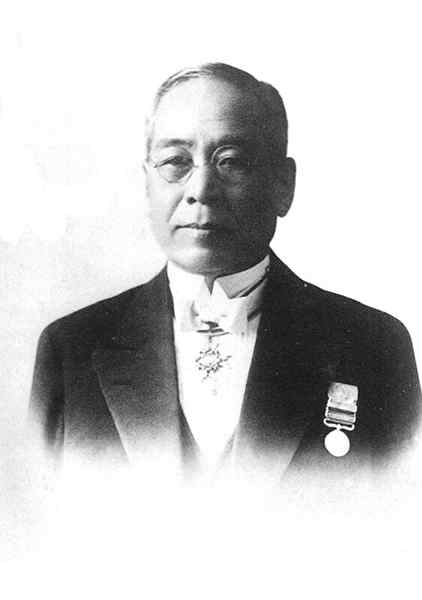
- 4509
- 1109
- Tizian Liebich
Er Toyotismus, Toyota -Produktionssystem (TPS) oder Lean Manufacturing (Herstellung ohne Abfall) ist Eines die drei Hauptparadigmen für Produktionssysteme, die als Reaktion auf die besonderen Umstände entstand.
In diesem Sinne sind viele seiner grundlegenden Konzepte uralt und exklusiv für Toyota. Andere haben ihre Wurzeln in traditionelleren Quellen. Diese wurden als Best Practices in vielen weiteren Branchen übernommen, jenseits der Automobilproduktion.
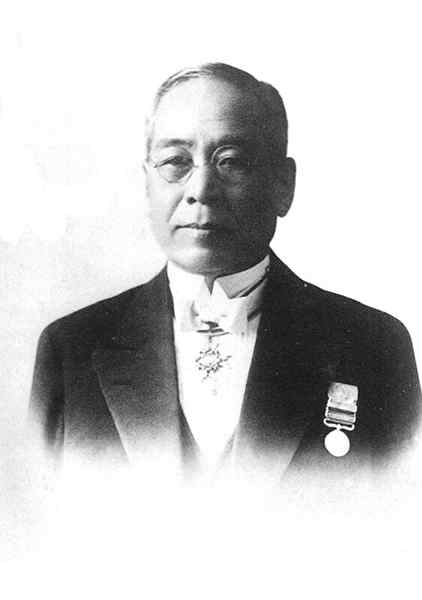
Das Toyota -Produktionssystem wird hauptsächlich in großen Unternehmen eingesetzt, die auf die Massenproduktion konzentriert sind. Seine charakteristischen Merkmale sind das Management ohne Abfall (Schlankes Management) und Produktion ohne Abfall (Schlanke Produktion).
Im Jahr 1990 etablierte eine gut bekannte Studie des Massachusetts Institute of Technology die Erfolgsfaktoren von Toyota. Dies waren technologische Führung, Kostenführung und Zeitführung.
Der Unternehmensansatz und die grundlegende Strategie des Unternehmens betrachten die Fabrik als vollständiges System. Das heißt ein Arbeitssystem, das einzelne Workstations und Workshop überlappt.
[TOC]
Geschichte des Toyoyismus
1902 erfand Sakichi Toyoda einen Webstuhl, der jedes Mal, wenn er feststellte, dass ein Faden gebrochen war. Dies verhinderte, dass defektes Material geschaffen wurde.
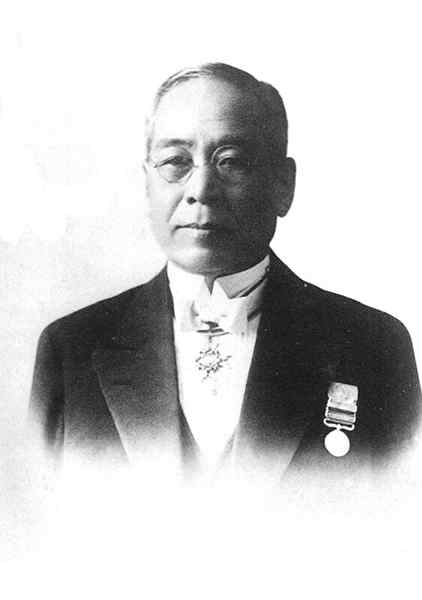
Später, im Jahr 1924, erstellte er ein automatisches Webstuhl, mit dem eine Person mehrere Maschinen betreiben konnte. Dies war der Ursprung eines der Begriffe des Toyotismus: die Jidoka. Das Konzept bezieht sich auf die Qualität des Produktionsprozesses und die Trennung des Menschen und der Multipro -Process -Managementmaschine.
Dann schuf Sakichi eine Automobilfirma, die für Kiichiro Toyoda, seinen Sohn, verantwortlich war. Im Jahr 1937 kiichiro acuña die Phrase gerade rechtzeitig (rechtzeitig (Gerade rechtzeitig).
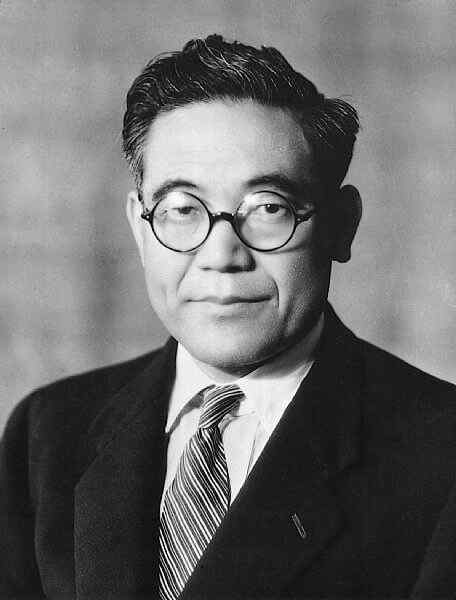
Aus mangelnder Fonds konnte das Unternehmen kein Geld verschwenden, das über Ausrüstung oder Materialien in der Produktion hinausging. Alles sollte rechtzeitig richtig sein, nicht zu früh oder zu spät. Dies wurde das zweitwichtigste Gebot des Toyotismus.
Kann Ihnen dienen: VerwaltungsmanagementNach dem Zweiten Weltkrieg beauftragten sie den Ingenieur Taiichi Ohno, die betriebliche Produktivität zu verbessern und die Konzepte von gerade rechtzeitig und zu verwalten Jidoka. Er wurde zum Manager des Maschinengeschäfts einer Motoranlage ernannt und experimentierte zwischen 1945 und 1955 mit vielen Konzepten in der Produktion.
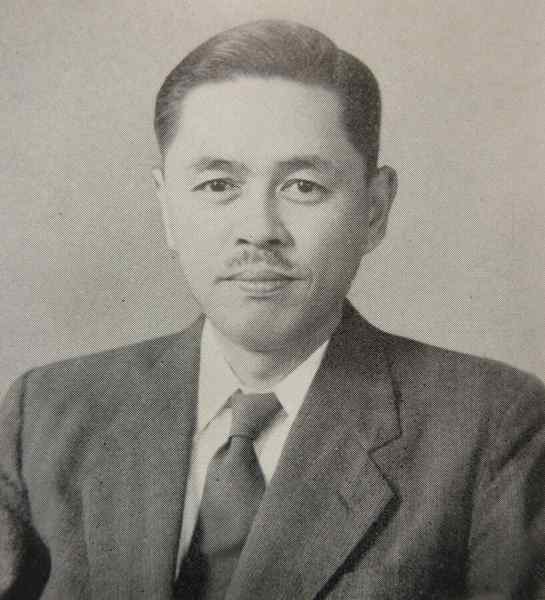
Seine Arbeit und seine Anstrengung sind in hohem Maße, was zur Formulierung des heutigen Toyota -Produktionssystems geführt hat.
Eigenschaften des Toyotismus
Eines der Eigenschaften des Toyotismus ist die Produktion kleiner Grundstücke. Die Arbeit in jeder Phase des Prozesses wird nur durch die Nachfrage nach Materialien der nächsten unmittelbaren Stufe bestimmt. Dies reduziert die Kosten für die Bestandsanwartung und die Lieferfristen.
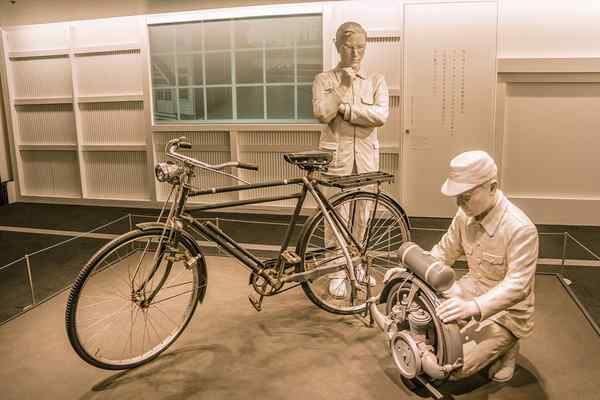
Andererseits werden Arbeiter in Teams geschult. Jedes Team hat Verantwortung und Schulungen, um viele spezielle Aufgaben auszuführen.
Sie führen auch die Reinigung und Reparatur kleinerer Geräte durch. Jedes Team hat einen Führer, der als einer von ihnen auf der Linie arbeitet.
Darüber hinaus müssen die Arbeiter Produktfehler so schnell wie möglich entdecken und korrigieren. Wenn ein Defekt nicht leicht reparieren kann, kann jeder Arbeiter die gesamte Linie stoppen, indem ein Kabel gezogen wird.
Schließlich werden Lieferanten als Partner behandelt. Diese werden geschult, um die Vorbereitungszeiten, Lagerbestände, Mängel, Fehler der Maschine und andere zu verkürzen.
Was sind die Phasen des Toyotismus??
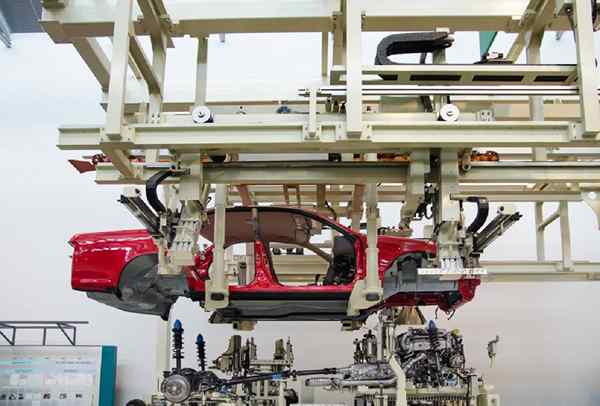
Das Toyota -Produktionssystem kann in 3 Phasen unterteilt werden:
Design eines einfachen Fertigungssystems
Produktionssystemfluss sollte keine Unterbrechungen aufweisen. Dies kann erreicht werden, wenn das fertige Produkt einen schnellen Rohstoffstrom vorliegt.
Es kann Ihnen dienen: Prinzipien der VerwaltungskontrolleMan (Betreiber) und die Maschine (Ausrüstung) müssen systematisch entsprechend den Kundenanforderungen ausgeglichen werden.
Identifizierung von Räumen für Verbesserungen
Das ultimative Ziel ist ein System, das einen gleichmäßigen Materialfluss hat und gleich.
Ständige Verbesserung
Ein wesentlicher Aspekt des Toyotismus ist die Flexibilität der Ausrüstung und die Fähigkeit, es mit der Flexibilität des Produkts auszurichten. Dies ermöglicht es, schnell auf die Kundenanforderungen zu reagieren und gleichzeitig rechtzeitig ein Hersteller zu sein.
Vorteile
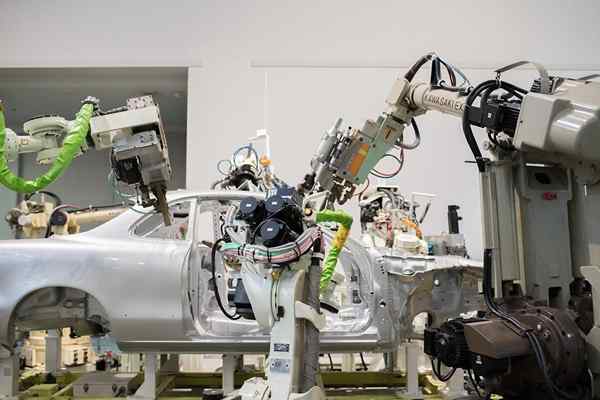
Reduziert Abfall
Einer der Vorteile des Toyotismus ist, dass es versucht, alle Formen von Abfällen zu minimieren. Dies schließt von den Materialstörungen bis zur Ergonomie des Arbeiters ein.
Suchen Sie nach Effizienz
Die Umweltbedingungen, die Arbeitseffizienz verhindern. Mitarbeiter nehmen aktiv an Verbesserungsprozessen teil. Dies verstärkt sein Zugehörigkeitsgefühl und erhöht seine Motivation.
Senkt die Kosten
Andererseits die Strategie gerade rechtzeitig ermöglicht eine bessere Nutzung der Ressourcen des Unternehmens. Es hilft auch einem höheren Cashflow. Die Speicherbedürfnisse werden reduziert und mit diesen Kosten verringert.
Der im Speicher gespeicherte Platz kann zum Hinzufügen neuer Produktleitungen verwendet werden. Und das Personal hat mehr Zeit, um schnell auf Änderungen der Kundennachfrage zu reagieren.
Nachteile
Es ist notwendig, Verbesserungen zu bewerten
Produktivität und Abfallüberwachung können die für die Produktion verwendete Zeit beeinflussen. Der Wert der Verbesserungen muss untersucht werden. Wenn die Leistung in einem Abschnitt es schafft, größer als die eines früheren Stadiums, wurden die Ergebnisse nicht verbessert.
Kann Ihnen dienen: Drehung der zu zahlenden Konten: Formeln, Berechnung, BeispieleFunktioniert besser mit stabilen Komponenten
Ebenso ist ein weiterer Nachteil, dass die Prinzipien von gerade rechtzeitig Sie arbeiten besser mit stabilen Systemkomponenten. Jede Einschränkung, die nicht bei der Planung gezählt wurde, gefährdet möglicherweise das gesamte System.
Beispiele für Unternehmen, die Toyotismus verwenden
Das klassische Beispiel für Unternehmen, die dieses System verwenden, ist natürlich das Toyota -Unternehmen. Die Toyotismus -Philosophie hat dazu beigetragen, dass dies eines der wichtigsten Automobilunternehmen weltweit ist. Dieses Konzept wurde weltweit repliziert.
Eines der Unternehmen, die die Strategien des Toyotismus umgesetzt haben, ist John Deere. Dieser Hersteller von landwirtschaftlichen Maschinen tätigte 2003 eine wichtige Investition, um seinen Betrieb in Iowa, USA, umzuwandeln.
Diese Praktiken haben es Ihnen ermöglicht, Aktivitäten ohne Mehrwert zu identifizieren und sie so weit wie möglich zu beseitigen.
Verweise
- Haak, r. (2003). Theorie und Management von kollektiven Strategien im internationalen Geschäft: Die Auswirkungen der Globalisierung auf die japanischen deutschen Geschäftskollaborationen in Asien. New York: Palgrave Macmillan.
- Die Kunst von Lean. (s/f). Toyota -Produktionssystem grundlegendes Handbuch. Abgerufen am 7. Februar 2018 von Artoflean.com.
- 1000 Unternehmen. (s/f). 7 Prinzipien des Toyota -Produktionssystems (TPS). Abgerufen am 7. Februar 2018 von 1000vers.com.
- Shpak, s. (s/f). Vor- und Nachteile der Lean -Produktion. Abgerufen am 7. Februar 2018 von Smallbusiness.Chron.com.
- Basak, d.; Haider, t. Und Shrivastava, zu. K. (2013). Die strategischen Schritte zur Erreichung der Lean Manufacturing Systems im modernen Betriebsmanagement. Internationales Journal für Informatik- und Managementstudien, Vol. 13, nein. 5, pp. 14-17.
- Globale Fertigung. (2014, 11. Juni). Top 10: Lean Manufacturing -Unternehmen auf der Welt. Abgerufen am 7. Februar 2018 von ManufacturingGlobal.com.
- « Quechua Literaturgeschichte, Merkmale und Vertreter
- Maya -Literaturgeschichte, Eigenschaften, Autoren und Werke »